POINT OF USE INVENTORY CONTROL
It is products and technology that provide a total solution for the management and streamlining of supply chains and inventory control at the point-of-use of consumables and tools.
Consumables:
All Business or Industrial processes use [or consume] a range of ‘items’ as inputs to their own process. These items constitute their input inventory. Industrial workers use Personal Protection Equipment [PPE] such as gloves,
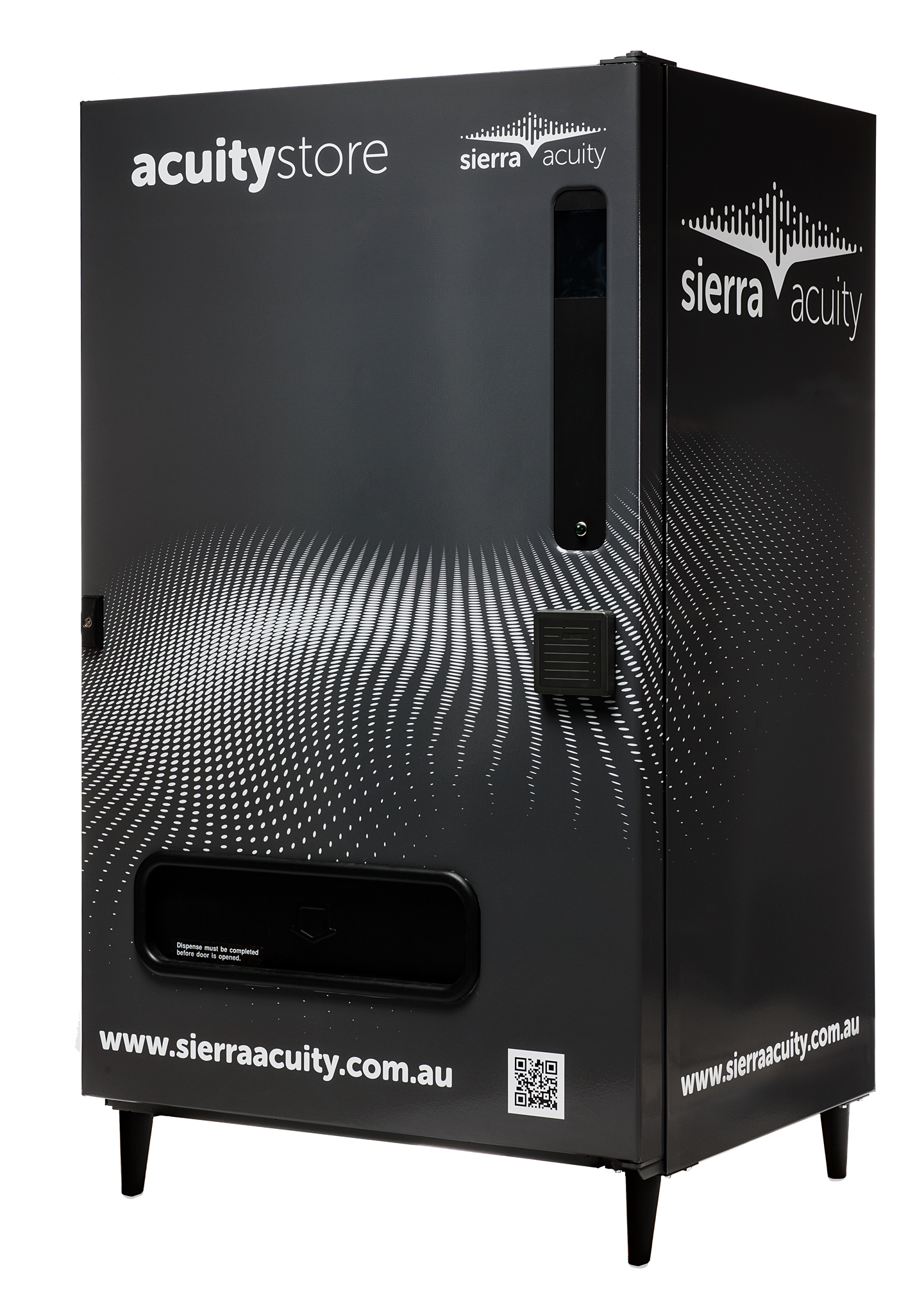
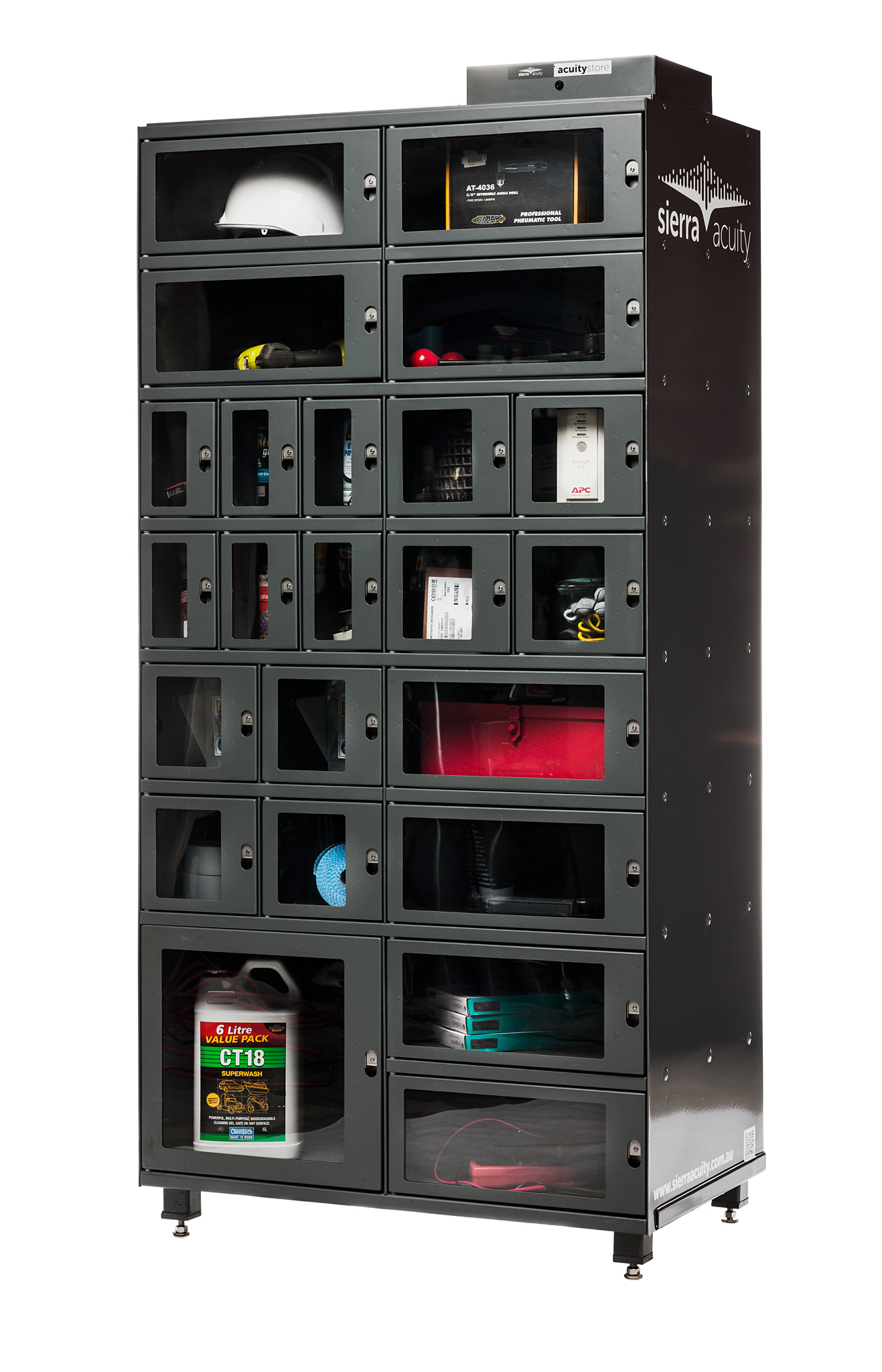
Point of Use:
“Walk Time”: Where items are kept in a Central Store, employees must go to the Store to retrieve what they need before carrying on their tasks. A recent study at a Boeing Aircraft Maintenance facility in the USA showed that the average Mechanic walked more than 5 Km per day retrieving the tools needed for work, resulting in a significant loss of working time. A study at Tractor manufacturer John Deere showed that, from “tools down” to “tools up”, each trip to the Tool Store “cost” John Deere more than 30 minutes of productive time. Consumables are critical to the Business Process of any
BENEFITS
Having the stock always available and within reach has been found worldwide to lead to a reduction in consumption (or waste) of many supplies. The automatic stock count and re-order process eliminates much of the overhead associated with provisioning and stocking the consumables. The dispensing machines are thus proving to be highly successful in providing substantial, continued hard-dollar savings in inventory provisioning and consumption.